Extract Midsurfaces
Use the Automatic tool to extract the midsurface of sheet metal stampings, molded plastic parts with ribs, and other parts that have thickness clearly smaller than width and length.
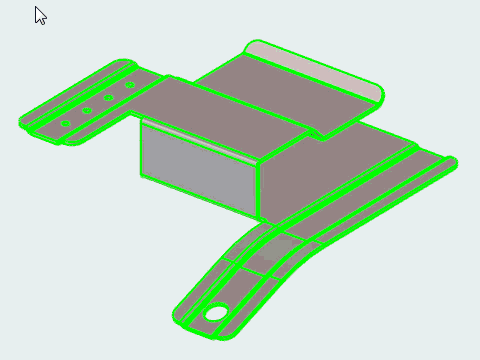

Automatic Options
- Destination component
- Select which component newly created midsurfaces are placed in.
- Mask input geometry
- Hide input midsurfaced geometry in the modeling window upon exiting the context.
- Extract across components
- Extract the midsurface of one component at a time.
- Clear existing plates
- Clear existing plates prior to midsurface extraction.
- Midsurface method
- Select a method for midsurfacing.
- Offset midsurface position
- Select a method for positioning midsurfaces when the thickness of thin solids is inconsistent.
- Align steps
- Select a method for offsetting the midsurface.
- User-specified
- Change the offset of the midsurface, using a value from 0 to 1, in order to specify the offset from the largest side of the volume.
- Use base surfaces
- Use base surfaces info for midsurface extraction.
- Cleanup tolerance
- Select a method for defining the cleanup tolerance.
- Maximum R/T ratio
- If the maximum R/T ratio (radius/thickness) is greater than this value, then that section of the solid will not be midsurfaced.
- Define thickness limits by
- Select a method for defining thickness limits.
- Max/Min thickness
- Change the min/max thickness ratio for midsurface extraction. This is the highest acceptable ratio of the thickest plate’s thickness to that of the thinnest plate. Thicknesses above this ratio are ignored.
- Minimum thickness
- Change the minimum thickness of the plates in the part that should be midsurfaced. Plates with a thickness smaller than this value will not be midsurfaced.
- Maximum thickness
- Change the maximum thickness of the plates in the part that should be midsurfaced. Plates with a thickness greater than this value will not be midsurfaced.
Keyboard Shortcuts & Mouse Controls
To do this | Press |
---|---|
Exit tool | Esc |