Parameter Settings
Setup the geometry cleanup and defeaturing parameters in the Criteria and Parameters Files Editor dialog, Parameter tab.
These parameters are used to define things such as washer layers around holes, defeaturing pinholes and solid holes, rows of elements along fillets, and many other options.
The Parameters tab is divided into multiple sections. Each section can be toggled to
show or hide its options via the small triangular arrow () to the right of it.
Each section represents a specific type of operation, which can be enabled or
disabled at several levels.
Element/Import

Figure 1.
- Target element size
- Desired element size for meshing and optimization.Note: The element size defined here should match the ideal value for min length and max length as defined in the criteria file. If this does not match, Batchmesher may not be able to produce meshes that adhere to the target quality requirements.
- Import model with tolerance
- Tolerance value to be used while importing the CAD model.
Extract Midsurface
The Extract midsurface parameters define the tasks that are performed by Batchmesher when extracting the midsurface.
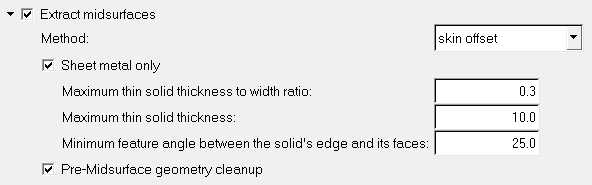
Figure 2.
- Method
- Select method to use when extracting the midsurface before meshing.
- Sheet metal only
- Only consider geometry for midsurface extraction that meets the user
defined settings for the options specific to sheet metal.Note: If this option is disabled, it will result in a time savings, but all parts will be attempted to have a midsurface extracted.
- Maximum thin solid thickness to width ratio
- Maximum ratio between the approximate thickness of the thin solid part (shortest dimension) and its approximate width (2nd shortest dimension). This parameter is used to limit the midsurface extraction to parts for which the thickness is clearly smaller than the length and width.
- Maximum thin solid thickness
- Ignore thin solids with a thickness less than the specified value during midsurface extraction.
- Minimum feature angle between the solid’s edge and its faces
- Minimum angle used to distinguish top and bottom faces of a thin solid from its sides. Angles less than the specified value will be treated as if they were flat for purposes of midsurface extraction.
- Pre-Midsurface Geometry cleanup
- Perform geometry cleanup steps on the model before midsurface extraction.
Direct Midmesh
The Direct Midmesh parameters defines settings used to create direct midmesh.
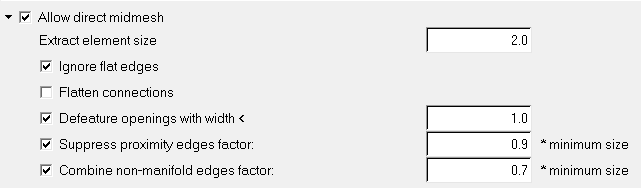
Figure 3.
- Ignore flat edges
- Do not imprint flat edges from the input geometry onto the midmesh.
- Flatten connections
- Align/flatten the midmesh at ribs/connections.
- Defeature openings with width <
- Remove small holes and openings less than the specified width.
- Suppress proximity edges factor
- Remove 1D topology edges within the given factor of the minimum size from the criteria file.
- Combine non-manifold edges factor
- Join non-manifold edges within the given factor of the minimum size from the criteria file.
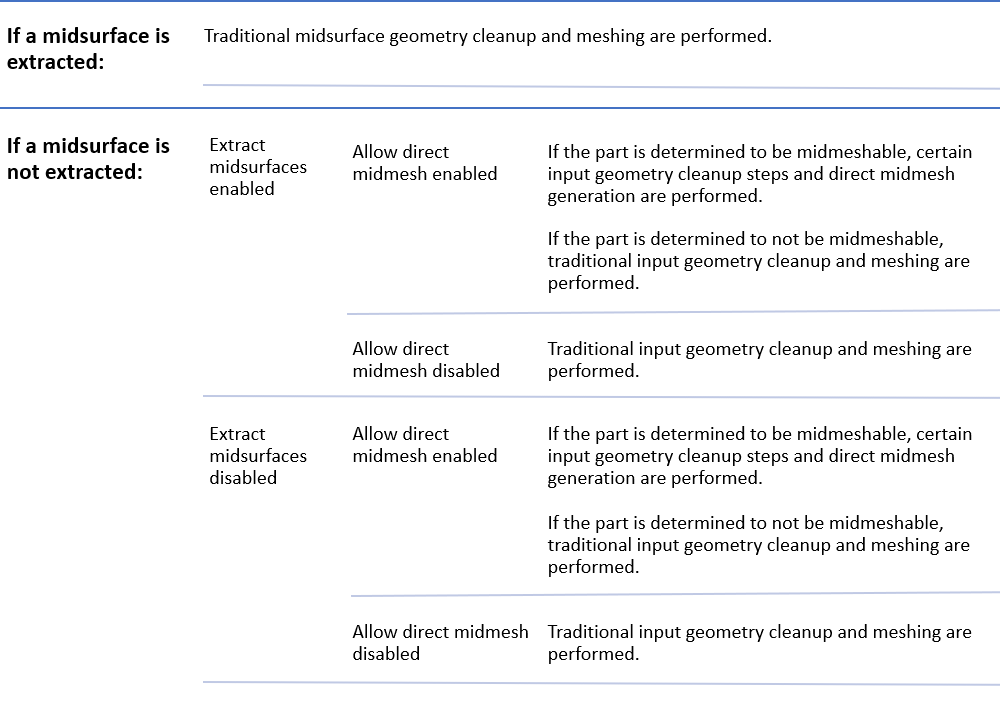
Geometry Cleanup
Geometry cleanup parameters define a variety of geometry feature recognition and preparation tasks performed by Batchmesher.
Geometry cleanup behaviors and options provide excellent feature capture with more user control resulting in more predictability, consistency and ease of use.
Batchmesher recognizes classified features like beads, dimples, flat bottom bosses/depressions, flanges, fillets, holes (2d and 3d), and so on. These features are treated following user defined criterias, allowing the preservation of the main feature edges providing excellent feature capture.
- Flat feature suppression level, a curvature based feature suppression.
- Suppress edges by proximity, allows to handle feature edges in close proximity, generally based on minimum element size.
Controlling the above parameters can result in good feature capture with minimum quality index failures. However, features are given more importance which might increase the failed element count based on geometry and the cleanup parameter values. It is important to define all of the settings appropriately.
Select the Geometry cleanup checkbox to enable additional cleanup parameters that can be turned on and off independently.
Surface Hole Recognition
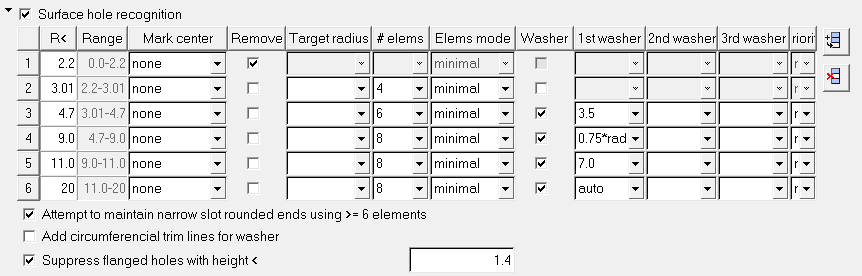
Figure 4.
- Surface hole recognition table data
- Define radii ranges and additional options in the table. Click
to add a row to the table, or click
to remove a row from the table.
Table 1. Surface Hole Recognition Table Data Column Action R< Maximum radius of the current hole range. The minimum value is taken as 0.0 for the first row, or as the maximum value from the previous row. For slotted holes, the radius is measured at the tip of the hole. Range Radius range for the current row. This value is read-only. Mark center Create a node and tag at the center of the hole, or do nothing. Remove Remove (defeature) the hole. For slotted holes, the hole is removed only if the tip radius is less than the specified radius threshold, and the length of the hole is less than 1.4 times the target element size. If Remove is disabled, additional options are available. Target radius Adjust holes in the range to have the specified target radius. The radius can be specified as an exact value, for example 5.0, or as an expression based on the original radius, for example radius*1.1, radius-0.5, radius+0.5. # elems Enter the minimum/exact number of elements to create around the holes, or set to auto to automatically select the number of elements so that the min and max element size requirements are satisfied, with the best possible representation of the hole shape. Tip: Auto is not recommended for holes with washer layers.Elems mode Choose whether # elems setting defines the minimum or exact number of elements. Washer Create washer layers around holes. If specified, one or two layers can be created. 1st washer/2nd washer/3rd washer Sets the width of the first, second, third washer as a constant value (select the blank entry in the drop down and enter a value), a scale of the hole radius, for example 0.6*radius, a subtraction formula, for example 14.0-radius, or an automatic determination based on element quality. Priority Set the priority of one radii range over the others. For example, to ensure all bolt holes (radii 10-15) have correct washers but other holes are not critical, holes with radii 10-15 will receive higher priority than others. This ensures that if two holes close to each other in the model have overlapping/conflicting washers, the hole with higher priority gets the washer while the other does not, or the hole with the lower priority may get a modified washer instead. In addition, when a hole is set to high priority, washer elements are not modified to correct for failed element quality. If a hole is set to normal priority, washer nodes are allowed to move to correct the quality. - Attempt to maintain narrow slot rounded ends using >=6 elements
- Attempt to generate a mesh using the pattern indicated in Figure 5.
Figure 5.
Figure 6. - Add circumferencial trim lines for washer
- Keep geometry trim lines for washers.
Figure 7. Add circumferencial trim lines for washer - Off
Figure 8. Add circumferencial trim lines for washer - On - Suppress flanged holes with height <
- Recognize holes with small downward flanges and eliminate those flanges with a height less than the specified value. Flanges with a height less than the minimal element size are extended to the minimal element size if not removed.
Use File for Hole Recognition

Figure 9.
Batchmesher compares the defined locations to the holes in the model, and prioritizes the holes that match. All of the options for Surface hole recognition are available for these holes. If one or more holes files are defined, Batchmesher looks for the found holes in each file, in the order the files are defined. If found, it applies the washer table linked to the first found file to the corresponding holes. If a hole is not found in any file, the settings from the default general surface holes table are used.
Multiple files can be specified, each with their own definitions. The order of the files determines the order of precedence in the case where there are overlapping or conflicting definitions.
Click Add table to add a new table for creating a new hole file. Click Delete table to delete the specified hole file table.
1 1420 -839 65
2 1724 -846 212
3 1683 -845 265
4 1660 -841 308
Figure 10. Spaces/Tabs with Line Numbers1,1420,-839,65
2,1724,-846,212
3,1683,-845,265
4,1660,-841,308
Figure 11. Commas with Line NumbersSolid Hole Recognition
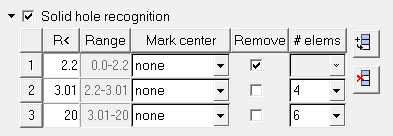
Figure 12.


Column | Action |
---|---|
R< | Maximum radius of the current hole range. The minimum value is taken as 0.0 for the first row, or as the maximum value from the previous row. |
Range | Radius range for the current row. This value is read-only. |
Mark center | Create a node and tag at the center of the hole, or to do nothing. |
Remove | Removes (defeature) the hole. If Remove is disabled, you must specify the minimum/exact # elems to create around the holes. |
Surface Fillet Recognition
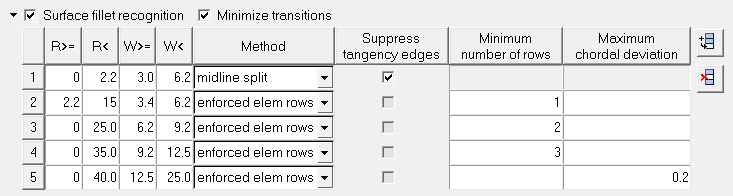
Figure 13.
- Prevent the main (long) edges of the fillets from being suppressed, and also prevent the nodes of those edges from moving while fixing element quality.
- Remove/defeature fillets. Gaps may result if complicated fillets cannot be removed.
- Split the fillets along the mid-line and suppress the edges.
- Specify the number of elements across the width of the fillets for given fillet radii.
- Specify the chordal deviation to be achieved while meshing.

Figure 14.
If the width or number of rows columns in the surface fillet recognition table are empty, the next default value will be applied. In this example, that means uniform fillet strips with an average fillet width between the element sizes of 0 to 2.0 will be meshed with one row of elements.
A fillet can be meshed with enforced rows of elements, or split at its midline and meshed accordingly based on element quality.
Flange Recognition
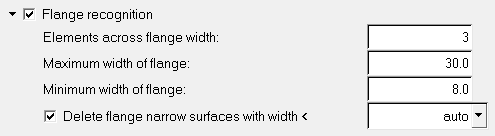
Figure 15.
- Elements across flange width
- Minimum number of elements to be created across the flange width.
- Maximum width of flange
- Maximum flange width to consider for flange recognition.
- Minimum width of flange
- Minimum flange width to consider for flange recognition.
- Delete flange narrow surfaces with width <
- Controls the removal of narrow flange surfaces to avoid creation of
sliver elements and disruptions in the mesh flow.
- Auto
- Delete narrow flange surfaces when the maximal narrow surface width is the minimum of 0.2*element_size and min_element_size.
- <value>
- Delete narrow flange surfaces when the maximal narrow surface width is the minimum of the specified value.
Figure 16. Flange Narrow Surface Width
Figure 17. Narrow Surface Removed
Bead Recognition

Figure 18.
- Suppress beads with height <
- Enable bead recognition and suppress any beads with a height less than the specified value. This helps eliminate small elements and aids in creating a good mesh flow.
- Preserve rounded bead midline
- Enforce node placement along the midline of a rounded bead.
Logo Recognition

Figure 19.
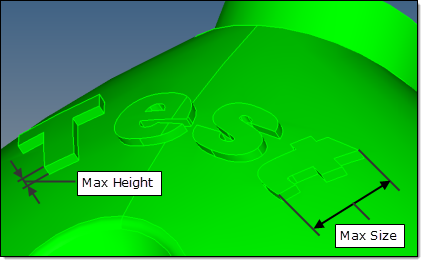
Figure 20. Logo Recognition Parameters
- Remove logo with size <
- Maximal size of a letter in the logo, as measured along/parallel to the "shiny" surface.
- and height <
- Maximal height/depth of a letter in the logo, as measured normal to the "shiny" surface.
- Concavity factor
- Creates a filter that provides more flexible control of automatic logo
recognition. As this is a heuristic tool, it may remove real features,
such as flat bottom round dimples, that were not intended for removal.
The Concavity factor is a quantitative measure of a letters shape
complexity, formally defined as:Tip: Extend the recognition and removal of a logo by reducing the Concavity factor.
Thread Recognition

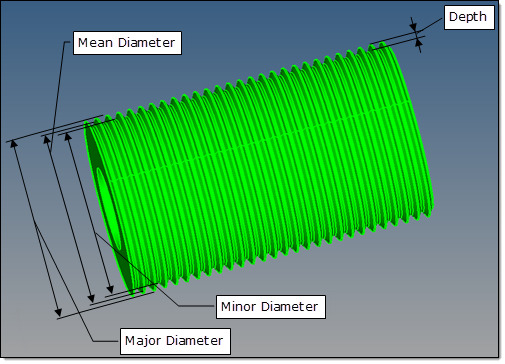
Figure 21. Thread Recognition Parameters
- Remove threads with depth <
- Remove cylindrical or conical threads with a depth less than the specified value, and replaces them with a smooth cylinder or cone surface.
- and replacing cylinder diameter
- Method used to define the diameter of the replacing cylinder or cone.
- autodecide
- Automatically determine diameter based on the diameter of a blank before thread cutting begins.
- major
- Use diameter of the thread major.
- mean
- Use diameter of the thread mean.
- minor
- Use diameter of the thread minor.
Other Options
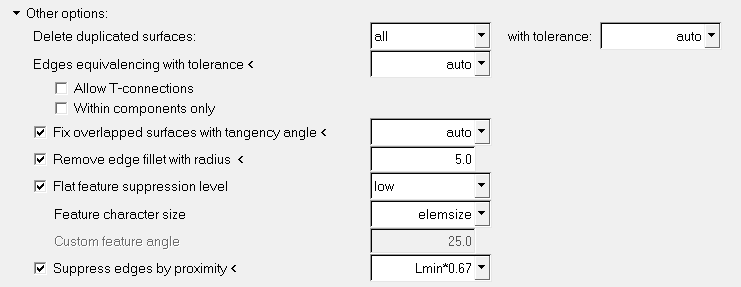
Figure 22.
- Delete duplicated surfaces / with tolerance
- Define which duplicate surfaces to delete before meshing.
- Edges equivalencing with tolerance <
- Tolerance to use for equivalencing (stitching) edges, in conjunction
with the options below.
- auto
- Calculate the tolerance internally.
- <value>
- Enter a tolerance. This is more useful when the auto tolerance is not sufficient to make all of the necessary connections.
- Allow T-connections
- Allow T-connections (non-manifold edges) to be created during the stitching process.
- Within components only
- Allow stitching only within components. Stitching between edges of different components is not allowed.
- Fix overlapped surfaces with tangency angle <
- Fix overlapping surfaces.
- Auto
- Calculate the tangency angle internally.
- <value>
- Enter a maximal tangency angle to fix overlapped surfaces.
Figure 23. Overlapped Surfaces Tangency Angle
Figure 24. Overlapped Surfaces FixedNote: This option may remove the surfaces that should not be deleted. For example, it may happen to surfaces with T-connections. Setting the angle to < 45 may help reduce such side effects.
Figure 25. Possible Side Effects of Fixing Overlapped Surfaces - Remove edge fillet with radius <
- Square off any fillets/rounded edges located on free edges and having radii below the specified value. This helps to create a good mesh pattern in such areas. For concave fillets, this means material is removed. For convex fillets, this means material is added.
- Flat feature suppression level
- Suppresses feature edges based on curvature break angle. For the ease of use, you can select a curvature break angle range, which varies from very low to very high.
- Feature character size
- Calculate the curvature break angle, which is defined by an element size or calculated automatically based on characteristic dimensions of the part.
- Custom feature angle
- Custom feature angle.
- Suppress edges by proximity <
- Suppress full or partial feature edges within the defined proximity value.
Preserve Boundaries between Components

Figure 32.
- Preserve boundaries between components
- Do not suppress or remove components' boundary edges during geometry cleanup, and do not move elements nodes across the components' boundaries. In some cases, maintaining boundaries for adjacent components that do not have any structural meaning would significantly worsen the element quality results.
Mesh Options
The Mesh Options parameters are used by Batchmesher to generate a mesh on the cleaned-up geometry.
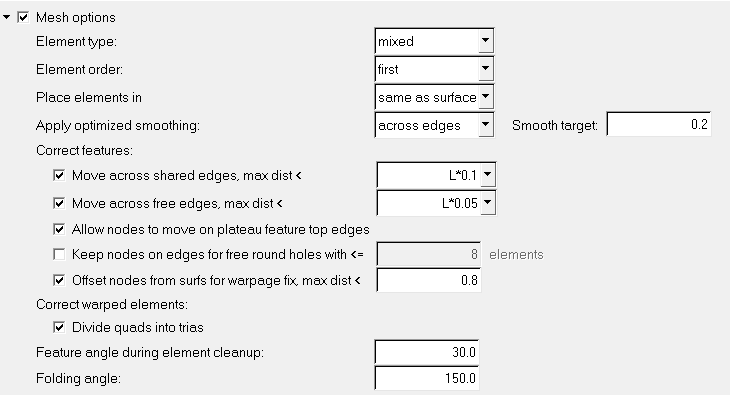
Figure 33.
Batchmesher has a powerful mesh flow algorithm which considers the shape of the geometry and aligns the mesh to create orthogonal meshes automatically. It also helps to reduce number of trias and places them strategically to avoid bad mesh patterns. Batchmesher is able to control the average element size in order to generate a more uniform mesh.
When Mesh options is activated, the following options become enabled.
These parameters control the behavior of the post-mesh element cleanup operations. They are intended to fix elements failing the quality criteria, to reduce number of tria elements for mixed/quad meshes, to correct bad mesh patterns, and to fix mesh flow for fillets. All of the element cleanup operations are compliant with the quality criteria, in that they should improve or at least not worsen the mesh quality.
- Element type
- Type of elements to create.
- Element order
- Create first or second order elements.
- Place elements in
- Organize new elements in either the current component or the original surfaces’ component(s).
- Apply optimized smoothing
- After the surfaces are appropriately meshed, the nodes are optimized
towards a target smoothing value to improve the element quality while
maintaining geometry features.
- none
- Do not perform smoothing.
- within surfaces
- Smooth the nodes within surfaces. Nodes on surface edges are not moved.
- along edges
- Smooth nodes both within a surface and along edges. Nodes on edges are allowed to move only along the edge to improve element quality.
- across edges
- Smooth nodes both within a surface and across edges. Nodes on edges are allowed to move both along and across the edge to the neighboring surface to improve element quality.
- Smooth target
- A composite Quality Index rating, ranging from 0 (perfect elements) to 1.0 (failed elements). The default of 0.2 is ideal for most cases, producing elements of good quality without taking too long to optimize, but can be altered if necessary.
- Move across shared edges, max dist <
- Move nodes across or away from the geometry's shared edges by less than the specified distance.
- Move across free edges, max dist <
- Move nodes across or away from the geometry's free edges by less than the specified distance.
- Allow nodes to move on plateau feature top edges
- Do not allow nodes to move off the top/bottom edges of recognized
embosses, particularly those containing central bolt holes to fix failed
elements.
Figure 34.
Figure 35. Allow Nodes to Move on Plateau Feature Top Edges = On
Figure 36. Allow Nodes to Move on Plateau Feature Top Edges = Off - Keep nodes on edges for free round holes with <=
- Do not allow any nodes to move off the edges of free holes (without
washers) with less than a specified number of elements. This is useful
if distortion of the holes is not allowed.
Figure 37. Keep Nodes on Edges for Free Round Holes with <= On
Figure 38. Keep Nodes on Edges for Free Round Holes with <= Off - Divide quads into trias
- Split quads into trias to meet the element criteria defined in the criteria file.
- Feature angle during element cleanup
- Element feature angle to maintain while performing element cleanup.
- Folding angle
- Elements whose angle exceeds this value are considered folded over, and BatchMesher attempts to clean them up.
Special Component Selection
The Special component selection parameters define a method for selecting special components.
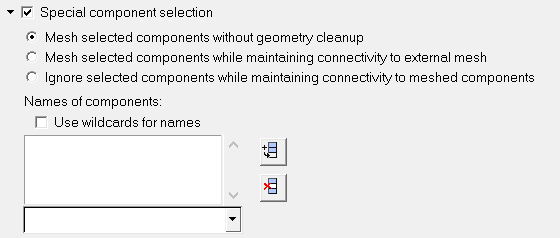
Figure 39.
- Mesh selected components without geometry cleanup
- Mesh the listed components but will not perform any geometry cleanup on them before meshing. Any remaining components that are not listed will be batch meshed using the normal process, including geometry cleanup.
- Mesh selected components while maintaining connectivity to external mesh
- Mesh the listed components while maintaining connectivity to any existing mesh.
- Ignore selected components while maintaining connectivity to meshed components
- Ignore the listed components while maintaining connectivity to any existing mesh. The mesh and geometry of the ignored components are not touched during batch meshing. The mesh created on other adjacent components is connected to any existing mesh on the ignored components.
Click to add
the name of a component specified in the drop down to the table. To provide a new
name, select the empty entry in the drop down and type a new name. Click
to
remove the selected row from the table.
- Create two sets of parameter/criteria files.
- The first should have a target element size of 10 and the appropriate parameters. In this parameter file, turn on the Special component selection option, Mesh selected components while maintaining connectivity to external mesh sub-option, and add front_10 to the component list.
- The second file should have a target element size of 20 and the appropriate parameters. In this parameter file, turn on the Special component selection option, Mesh selected components while maintaining connectivity to external mesh sub-option, and add rear_20 in the component list.
- Create a mesh type and assign the first set of criteria and parameter files.
- Create a second mesh type with the same name as the first, and assign the second set of criteria and parameter files.
- Choose the geometry file to be batch meshed, assigning it the mesh type from above, and submit the job.